Hospital and healthcare facilities are common projects for Egan’s 12 specialty trades. So much so, in fact, that a recently discovered article from Egan’s archives depicts just that: a new Shriners Children’s Hospital being erected in Minneapolis, with Egan’s (then called Egan & Sons) Mechanical team playing an integral role in the plumbing, heating, cooling, and medical gas systems within the building.
While the story itself may seem typical at first glance, in the more than 30 years since the hospital was built and the article was written, many things have changed in the cities in which we work, and the way in which we build them.
THEN AND NOW: WHAT’S DIFFERENT?
Egan continues to work on many different healthcare facilities, from new construction and renovations to electrical service calls and everything in between. What’s different, however, is the way teams approach the work.
The most obvious difference in the way the industry has evolved is in the shift from hand-drawn project plans to digitized versions. This has enabled increased collaboration among project teams, reduced risk for human error, and more efficient operating costs and timelines for projects.
The historical article depicts the old ways of coordinating project drawings:
Egan Air is also responsible for coordinating drawings for all of the trades. Gary Hunt, their draftsman, produced the drawings on Egan Air’s new computer aided drafting machine. Joel Bohach, Egan & Sons, then overlays the heating and cooling piping so that only minimal interferences are encountered by the men in the field. Some of the areas in this two story hospital are so congested, that without this coordination most people would wonder if the project would ever be completed on time.
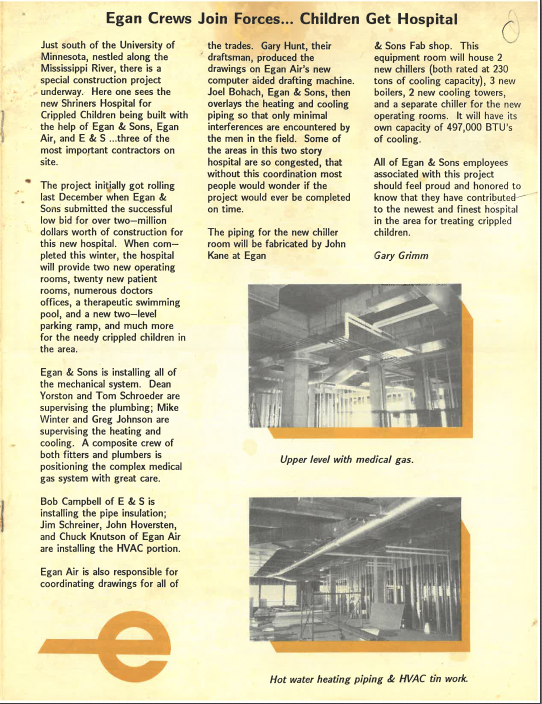
Today, a single modeler or a team of drafts personnel can work on project drawings and modeling without any need for hand-drawn coordination or overlays from other trades. By working exclusively with 3D modeling and computer aided drafting, Egan can collaborate with trades professionals and even other contractors to ensure the schematics are accurate and available to everyone on the project.
SURPRISING SIMILARITIES
Comparing the Shriners Hospital to a modern project such as M Health Fairview in Minneapolis, Minn. reveals many similarities between the two. Since the building of Shriners in Minneapolis, Egan has worked on dozens of hospitals and healthcare facilities throughout Minnesota, including Essentia in Duluth and Mayo Clinic in Rochester. The project scopes of these jobs are very similar, as hospitals continue to build and upgrade their facilities, using much of the same equipment now as they did back then to meet patient needs.
Prefabrication in the construction industry has been around for decades, and Egan has been leveraging our prefab shops on nearly every project to promote accuracy, quality, and safety. The article is a testament to Egan’s longstanding commitment to innovation, quality, and safety as the featured project utilized prefabrication for the chiller room piping.
Today, Egan’s fabrication efforts have expanded greatly, resulting in a new prefabrication facility currently under construction in Kasson, Minn. As was the case three and a half decades ago, prefabrication saves time and money on projects, while increasing safety and quality.
ALWAYS IMPROVING
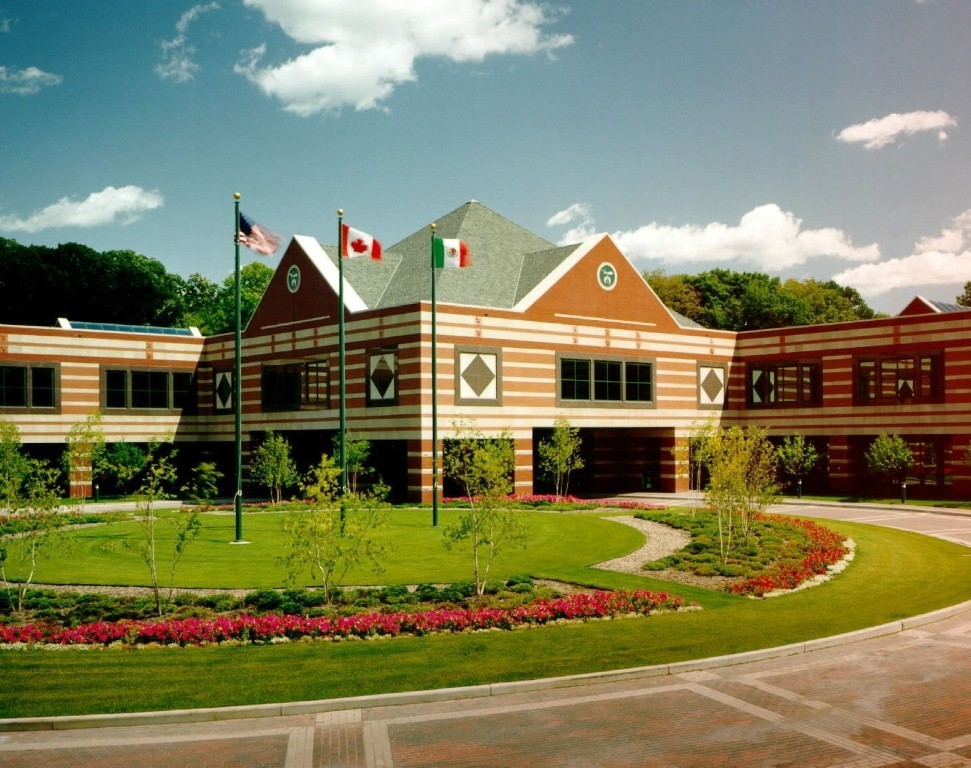
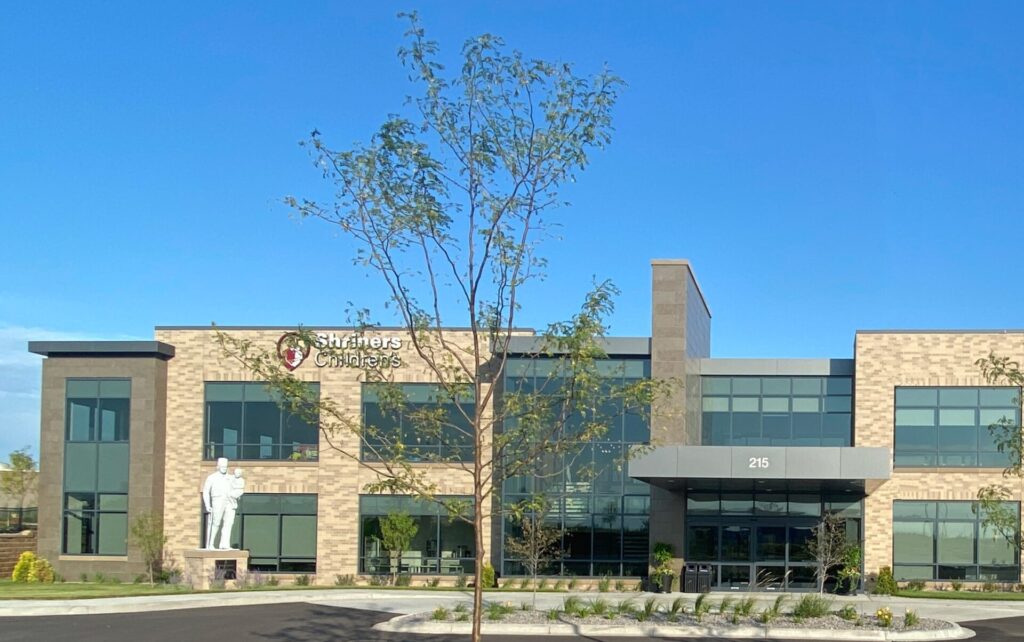
A lot can change in 30 years. Since the project in 1989, Shriners Children’s Hospital has moved to a new state-of-the-art facility in Woodbury, Minn., while the original building is now used by the University of Minnesota. Technological advancements, increased safety standards, and new business groups have all arisen within Egan in the last four decades. What hasn’t changed in that time, however, are the high standards Egan brings to every project.
Whether it’s through prefabrication or the implementation of new technology, Egan’s goal is to find ways to deliver projects more efficiently, at a higher quality, and with no injuries. For the last 80 years, Egan has been able to deliver on our promises by doing so, and we remain committed to our customers’ success for the next 80 years and more.